ISI Water builds membrane based water treatment systems. These are used around the world to treat many different type of water in many different types of industries. Uses include fish processing, mining, petroleum processing, municipal and resort water supplies etc. These different industries generally have very specific requirement with respect to scope and design, often specifying the font on a wire label for example, or a preferred vendor, alloy or design arrangement. However, once the project is completed, the issue of spare parts typically arises, and the question is often “what do you recommend”. Or if it is specified, it might suggest that “one year spare parts to be included”. What is the appropriate response and what does this mean?
Over the years, we have tried a number of approaches. These include providing a fully priced spare parts list with the intent that the client would select that spares they want to see. This has not worked out very well because 1) the client does not reasonably have the experience to make this selection, and 2) putting the onus for the client to select the spare parts results in action-paralysis. They would like ISI Water to make this recommendation.
How do we make a recommendation when we often don’t have any information on the client’s operations budgets, nor any knowledge of how they intend to operate the system? When we propose what we consider is a reasonable list, the response might be “we cannot afford that” or similar. The resulting gap between what we would like to see on the shelf vs. what the client would like to purchase has been a difficult to address. We need a method that allows the client to make the determination of criticality, which is what is being asked of us when we are tasked with creating a spare parts list. The unwritten liability is that if a part fails and it is not on the purchase list, that we have failed the client. This has led us to use a decision tree on how comprehensive the spare parts inventory should be. Before we present that, we have learned some truths about spare parts over the years:
Some truths
Operational spares are often not a part of the capital cost budget. This is why after a project is nearly completed, we are asked to re-order a lot of components, which would have more efficient to supply as part of the overall project from the get go. This issue is nearly universal and exists in every industry sector.
While Clients are often happy to select to the best alloys or most efficient plant design, and understand that this will cost more, they are not happy to purchase spare parts. The willingness to spend money is generally a function of the budget source. Operations budgets are traditionally bare-bones. The result is that often very costly plants that include significant capital expenditure are often staffed with as few personnel as possible and with generally low training levels. Spares generally fall into this same line of thinking.
There is often confusion about warranty and spare parts. We find that often a client will declare that no spare parts are needed because “we have a warranty”. The confusion seems to lie in the distinction between compensation for a failed component versus its availability. Depending on the part, even if it is warrantied, it must be purchased and shipped and installed. This may take many weeks, and it is possible the plant might be offline during this entire period depending on the replacement period.
Spare parts, when they are supplied, are often abused and neglected. We have seen on many occasions’ customer management that correctly and proactively purchased shelf spare parts and set up an inventory, but were disappointed to find that these parts were not available when needed. This is often what I have come to call a Stockroom RIP, or Rust-In-Place event. Spare parts inventories are often found to be waterlogged, rusted, stripped of sub-parts, lost, stolen or otherwise neglected. We now try to address this issue by recommending early on that storage areas isolated from the process areas be included in the overall layout and design. These areas should include shelving and climate control. For larger plants, we recommend a high-value spares area that is segregated from the other equipment.
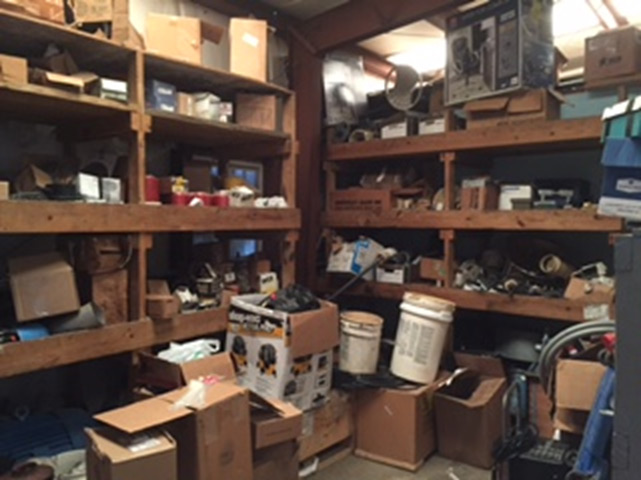
Spare Parts Dump. The good news was the equipment was separated from the process area– the bad news is that nearly everything was corroded, obsolete, including many broken parts that had been retained after failure and returned to the shelf.
The stockroom, which is where spare parts should be stored are often turned into equipment dumps where it is not possible to decipher what is new or old, what is outdated or obsolete, and what works and what does not.
To assist in the spare parts conundrum, we have come up with a simplified decision tree to assist in the determination of the stocking level needed for correct maintenance of the plant. A scale from 1-10 are used to determine calculate a spare-parts score. We have intersperse an example in “Blue”.
Test Questions for Determination of Percent Stocking Spares
- Are there technically capable people available to service the equipment, or do technical personnel have to travel to site to effect repairs?
0 We do all our own repairs
5 We can do most repairs but need assistance on some items
7 We have trouble retaining skilled employees for repair work, and when we subcontract it locally, the workmanship is often poor.
10 We cannot do any repairs and need assistance
- How quickly can I goods delivered to site from the manufacturer?
0 Very quickly
5 Several Days
7 Several days is typical although we can have delays due to customs or long holidays
10 Weeks
- What is the impact if the plant is offline? Are there alternate water sources that can be used?
1 We can meet our water requirement with the plant offline
2 We can meet our water requirements with an alternate source, although quality is much reduced.
5 We can meet some of our water requirement
10 We cannot meet any of our water requirement
- What is the cost if the water supply is interrupted?
0 There is little cost, we can wait it out
5 There is moderate cost
5 We pay more for local water deliveries and we don’t want to, but it is available.
10 There is high cost
- Is there a spare parts management system where new parts get ordered when they are consumed, where parts are stored properly and in climate control?
0 There is a good spare parts management system
5 There is no formal system but we can keep track
8 We don’t have a good management system. We sometimes can’t find spare parts or forget that we have used them up.
10 There is no system
After getting the results, sum them and multiply by 2x. ( In our example: 7 + 7 + 1 + 5 + 8 = 28 x 2= 56) This is the percent of total spares inventory budget that the Owner should have on site for spare parts. If the total recommended spare parts list might cost xx$, then the manager should budget 56% of that value. This budget figure can then be used to purchase the most likely maintenance items. Generally, these include electrical equipment (due to poor power quality) and controls equipment.
We are aware that this system is non-scientific, somewhat crude and includes flaws and can likely be improved. It is in fact barely scientific as compared to a mean-time-between-failure (MTBF) analyses, but practically these types of analyses are impractical for a small equipment customer. An obvious short-coming example might be that for one customer, downtime is so costly that they must have full spares inventory all the time irrespective of the “score”. This may be the case, but that client would be a good candidate for redundancy, which influences spare parts inventory. Redundancy, has the effect of buying time so that new spare parts can be purchased, shipped and installed and is often a design requirement.
Besides distance and criticality, sometimes location is a factor. For example, some sites have such notoriously poor power supply conditions where electrical equipment suffers high failure rates even with filtering and surge suppression. In these locations, motors, computers, VFDs etc. can have high failure rates. The selection of which parts in such a case relies on as much art and experience as any type of MTBF analysis.
Nevertheless, the exercise of generating a score tends to make plain the issues related to stocking and moves the decision making process from the supplier to the customer. It also serves to highlight some considerations that might otherwise have been overlooked. This process reduces the difficult task of trying to predict the failure rate of a plant that someone else is operating, and reduces the liability of trying to propose a budget for vendor parts will fail at some point in the future. Because it is rare for all spare parts to be purchased, it can focus the discussion on value and priority. If the Owner elects to not purchase our recommended spare parts list, and wishes to trim the budget, then this method provides a way to do that. The questionnaire could be expanded of course, and additional questions could be included which might assist in trying to pin down stocking spares and budgets for spare parts. For example: “are you feeling lucky?” We have plants in very remote areas with management deciding on zero spare parts inventory, and they’d been lucky, until one day they weren’t.